All You Need to Know About Offset Lithography
By Paul Bobnak | February 27, 2023
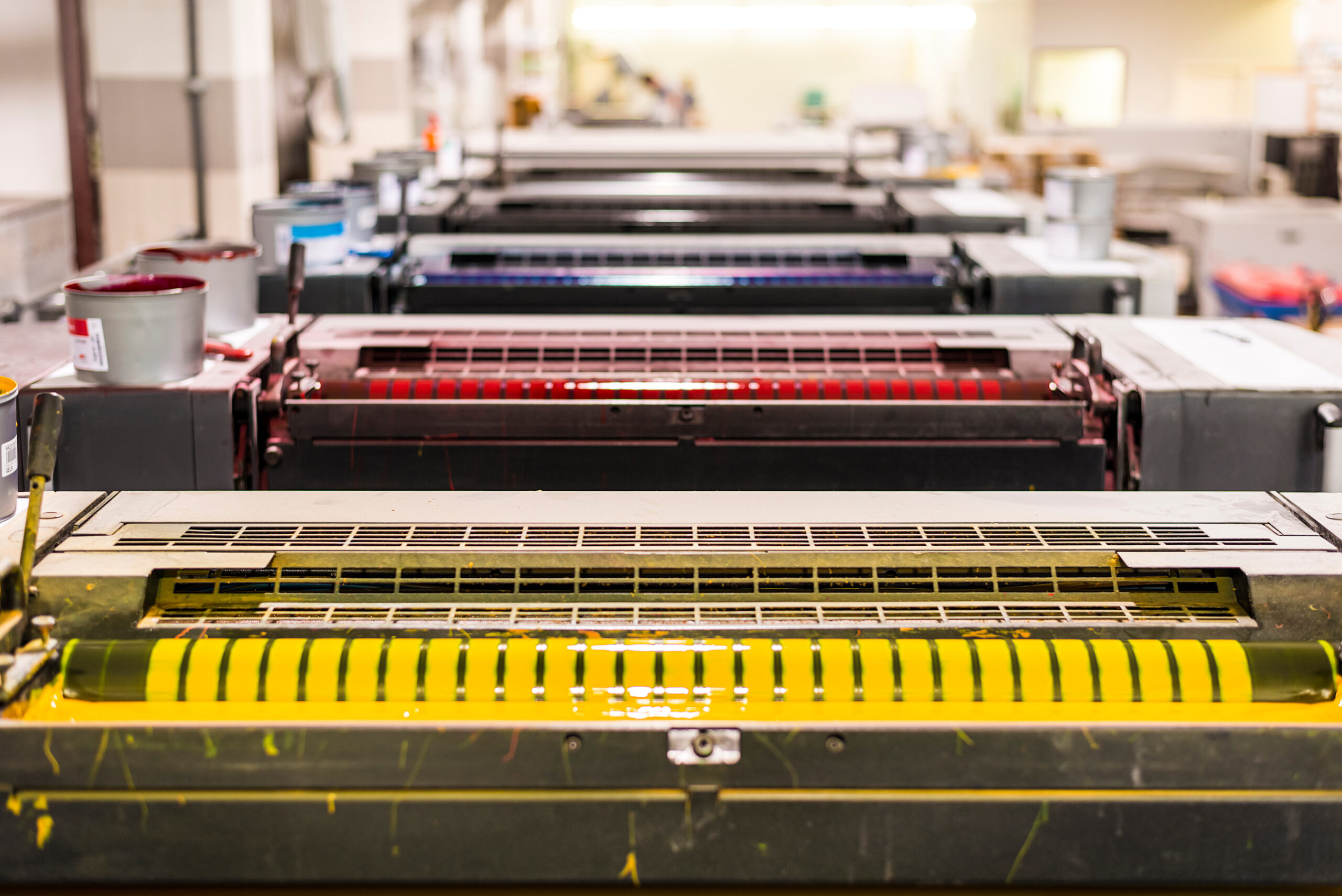
Individual printing methods have specific strengths and weaknesses that play a role in deciding which process to use in direct mail campaigns. In this article, we will look at one of the most popular processes, called offset lithography. We will consider the benefits of using offset, how the process works, and specific ways that the two main types are used in direct mail marketing.
What is Offset Lithography Printing?
Offset lithography is a printing process that transfers ink from a plate or cylinder to a blanket or rollers, then to paper, instead of directly from plate to paper. Of all plate printing methods, the majority of printing is offset.
A positive of an image and/or type is made on a plate, which can be metal, polyester, or paper. The plate is inked, then the image is offset onto a blanket, a kind of rubber plate. It is then offset again onto paper, either individual sheets or rolls. The two main types of offset lithography are web and sheet-fed. Factors like paper thickness, type of marketing campaign, budget, and deadlines may affect which method is the better choice in producing a direct mail piece.
Benefits of Offset Printing
Based on decades of experience, several advantages of offset make it a worthwhile and efficient choice. For example:
High Quality
Extreme detail and consistency result from controlling the ink flow across the plate.
Affordability
Using and reusing a single design means no retooling as well as saving time and money; in larger quantities, it also lowers the per unit cost.
Speed
Because plate set-up is quick, medium-to-large sized runs can be printed without delay. A fast ink drying system ensures that a project can be turned around quickly.
Versatility
Offset allows printing on a wide variety of substrates and objects in addition to paper, such as labels, containers, fabrics, plastic, canvas, and more.
Who Uses Offset Lithography Printing?
As noted above, offset lithography printing works best for producing high-quality materials in large quantities at an economical cost. So, some of the most common applications used include:
- Magazines
- Books
- Newspapers
- Brochures
- Catalogs
- Stationery
- Direct mail
In short, anything intended for a mass-market audience is best printed with offset litho.
Is there a Difference Between Lithography and Offset Printing?
In traditional lithography, a printing plate, originally a stone, was directly applied to paper to transfer an inked image. In time, aluminum or zinc plates replaced stones. Also, materials like rosin and talc were added to the process to help protect the plate’s image area and repel water from non-image areas.
In the offset lithography process, as described more in detail below, the image is transferred first from the printing plate to the rubber blanket, and then to the press sheet or roll. Unlike in the original method, the plate itself never comes in contact with the paper.
Types of Offset Printing
There are two main types of offset printing. Each has their advantages, but the main criteria for choosing one or the other are the run length and the finishing process to be used.
Sheet-fed printing presses are fed individual sheets of paper. The big advantage of this method is due to its cost-effectiveness. For nearly any quantity, sheet-fed is the most economical option.A large number of format sizes or sheet sizes can be fed individually through a press.
Web-fed or web presses are fed a continuous roll of paper which is cut at the end of the process. With a web press, depending on how it’s configured, you can do inline finishing and bindery, such as foiling, die cutting, perforating, gluing, folding, and binding. This method is most suitable for long run printing jobs or ones requiring quick turnaround or completion.
Understanding the Offset Lithography Printing Process
Lithography is a long process that in some ways, has changed little since it was invented in 1789. It starts with the important principle that water and oil do not mix.
Printing from a Flat Surface
The image areas and non-image areas are on the same plane.Each plate cylinder is customized based on the images and text which is intended to be printed onto the paper. A fountain solution pre-treats image areas to accept ink, which is sticky. At the same time, a dampening system distributes water in order to desensitize the non-image areas and reject the ink. When the plate cylinder spins, then, the ink will only stick to the image areas.
Transfer to the Blanket Cylinder
The offset cylinder has a rubber blanket around it that turns in the direction opposite to the plate cylinder. When the two cylinders roll against each other, water is squeezed off the plate and a mirror image is transferred to the blanket. This prevents moisture from damaging or distorting the paper in the final transfer.
Final Transfer to Paper
Finally, the impression cylinder, which turns opposite to the blanket cylinder, transfers the image (right-sided) to the press sheet (paper) when pressed against it. The compression provided by the blanket is especially useful for forcing ink onto crevices or grooves of rough-textured paper or other substrates.
Drying the Ink
Offset lithographic presses are either headset or coldset.
With heatset printing, printed materials are first run through or under a heating device, such as an oven or lamp. The solvents in the ink evaporate at high temperatures. As the paper passes over cooling rollers, the pigments remaining in the ink solidify. For projects using glossier or coated papers – such as direct mail – this is a better choice.
With coldset printing, inks dry through oxidation as well as absorption by the press sheet paper. For rough or more porous paper, this is a better choice.
Wrapping it up
When planning a direct mail campaign, it makes sense to include your printing method as one item on your services checklist. As we’ve examined here, offset lithography offers clear advantages for many types of printing and mail projects. Even with the rise of inkjet and digital, offset remains very widely-used.
Here at mailing.com, we have decades of experience in offset lithography. We look forward to working with you on designing a campaign that takes full advantage of our litho equipment to produce direct mail campaigns that meet your needs and solve your challenges. Feel free to contact us to talk all about it.